Plastic Bottle IV Solution Washing, Filling and Sealing Production Line
The XGF plastic bottle IV solution washing, filling and sealing production line mainly consists of three sections, including ionic wind washing or ionic wind and water washing section, constant pressure filling section and hotmelt sealing section. It can automatically complete procedures like bottle loading, bottle feeding and bottle turning by manipulator, ionic wind washing, bottle conveying, fixed quantity filling, cap collating, capping, simultaneously heating of cap and bottleneck, air eliminating, hotmelt sealing, bottle discharging, etc. This production line is primarily used for the production of both soft and hard PP plastic bottle IV solution.
- Production Capacity: 2000~20000 bottles/hour
- Bottle Specification: 50~500 ml round or irregular shaped plastic bottles
- Bottle Washing: ionic wind blowing
- Quantity of Washing: 20~60
- Quantity of Filling: 18~48
- Quantity of Sealing: 20~60
- Main Filling Medium: large volume infusion solution and other liquids
- Filling Error: ±1.5%
- Liquid Temperature and Pressure: 40~55 ℃ 0.6~2 kg/cm2
- CIP/ SIP: 125 ℃, 30 min
- Gas Consumption (clean air): Pressure: 0.6~0.8 Mpa 180(120) m3/h
- Cooling Water: 250 L/h, 15~20 ℃
- Noise: max. 75 dB
- Electric Capacity: 18~35 kW
- Due to the integration of washing, filling and sealing, the production line has compact structure and thus occupies small floor area. In addition, it is simply mounted and easily operated with high automation.
- The plastic bottle IV solution washing, filling and sealing production line adopts ionic wind washing, instead of water washing. The ionic air gun has the functions of monitoring failure and non-discharging. When there is no ionic wind, audio warnings will be given.
- The machine adopts PLC programmable controller with reliable performance.
- It comes with CIP and SIP systems, which help save cleaning time while ensuring sterilization effect. The cleaning and sterilizing time, pressure and temperature can all be easily adjusted on the touch screen.
- All parameters can be conveniently queried, altered and monitored on the touch screen. Operators can preset the maximum and minimum values of these parameters, so as to protect the machine from human errors during operation.
The conveying track and star wheel are directly connected. The clean compressed air helps accelerate the feeding speed.
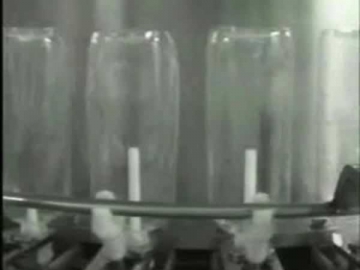
If there is no bottle in this station, it will automatically cut off the air and power source of the ionic air gun.
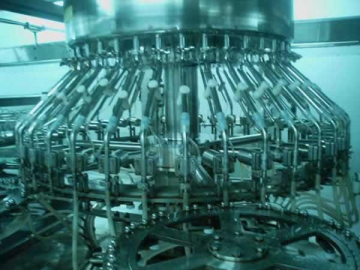
It incorporates constant pressure filling technique and world renowned brand filling valves. Each filling nozzle is equipped with a filling pipe to realize CIP and SIP.
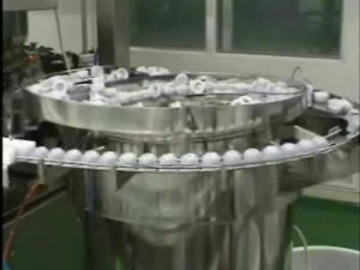
It collates bottle caps based on the electromagnetic resonance principle. It will automatically stop when there is no bottle.
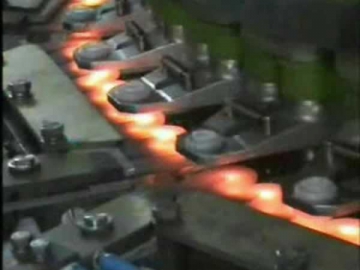
It seals by heating continuously and rapid pressing, which ensures good quality and smooth sealing. The heating part consists of two layers respectively used for bottle heating and cap heating. Heating temperature and time are adjustable.
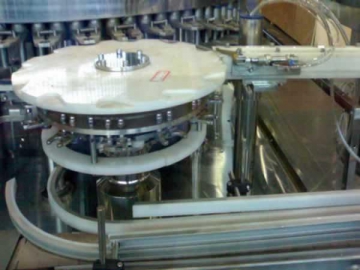
After cap welding, the bottles are delivered to bottle discharging track by star wheel. When manipulator is open, the discharging track will take away bottles.
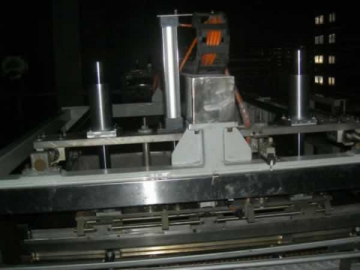
It consists of a manipulator used to place plastic bottles in sterilizing trays.
8. Automatic Bottle Unloading Station
It is used to unload the bottles from the sterilizing trays to the delivery track.
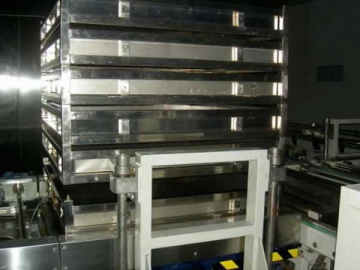
It is mainly used to remove sterilizing trays from the sterilization cycle system and pile them up.
IVEN Pharmatech is an experienced plastic bottle IV solution washing, filling and sealing production line manufacturer in China. Our company provides a wide range of products, including non-PVC infusion bag IV solution production line, vertical ultrasonic vial cleaner, vial labelling machine, and more.