Steel Wire Hot-Dip Galvanizing Line
As an advanced galvanizing equipment, our steel wire hot-dip galvanizing line comes with reasonable structure and a wide range of production capacity. The zinc-plating line will be described in detail below. Welcome to contact us for any questions.
Specification
- Steel wire: high/middle/low carbon steel
- Diameter: 0.8~1.6mm, 1.6~4.5mm, 4.5~8.0mm
- Plating thickness: 40~100g/m2, 150~450g/m2
- Wire number: 6~40 wires
- DV value: 35~150 mm•m/min
- Production capacity: 1000~20000 ton/year
Process flow of the steel wire hot-dip galvanizing line
Wire feeding (disk type/spool type) - thermal treatment (anneal/degrease, quenching) - degrease (hot alkaline rinse/ electrolytic alkaline rinse) - water rinse - acid rinse -flux solution - drying - hot-dip galvanizing (electricity/natural gas/ liquefied petroleum gas) - wiping (composite force/nitrogen/oiled charcoal/ asbestos clip) -air/water cooling - post treatment (passivation/waxing) - wire take-up machine (inverted type/spool type/horizontal type)
Wire pay-off machine
Disk type wire pay-off machine, vertical spool type wire pay-off machine, and horizontal spool type wire pay-off machine are all available for our steel wire hot-dip galvanizing line, while the first two kinds are passive type pay-off machines. A damping tension-adjusting gear is used for the stable feeding of the steel wire in this continuous galvanizing line.
Spool type wire pay-off machine
Vertical spool type wire pay-off machine
Disk type wire pay-off machine
Horizontal spool type wire pay-off machine
Thermal treatment furnace
In our steel wire hot-dip galvanizing line, the low carbon steel annealing could be conducted by electric heating pipe type muffle furnace, gas fired heating pipe type muffle furnace, gas fired flame furnace. Generally, the quenching of high carbon steel wire is conducted by patenting or water bath quenching according to the applications.
Electrolytic degreasing bath
Hot alkaline rinsing bath
Electric annealing furnace
Gas fired annealing furnace
Degreasing bath
For the low speed production, hot alkaline rinsing is usually used for the degreasing of steel wire, sheet metal, and so on. The electrolytic alkaline bath degreasing is commonly used for high speed production. The degreasing bath tank is designed to be in an overflowing circulation type. The reinforced PP plates are used for the welding, and an extracorporeal circulation solution preparation tank is available in our steel wire hot-dip galvanizing line for ensuring the stability of the bath solution and facilitating the dirt cleaning.
Water rinsing bath
The bath is welded by the reinforced PP plate, and the overflowing circulation rinsing design and air knife are available. Thus the desirable cleaning performance can be achieved and the cleaning solution utilization rate is enhanced. Besides, the sewage from the steel wire hot-dip galvanizing line is also reduced to some degree.
Hot water rinsing bath
Water rinsing bath
Fumeless pickling bath
The bath is welded by reinforced PP plate, and four water screens are used for the sealing, ensuring that no acidic fume will leak out. Thus the production environment will be greatly enhanced. The bath comes with a fluid heating system to enhance the cleaning speed and hydrochloric acid utilization rate.
Enclosed type fumeless pickling bath
Fumeless pickling bath
Flux solution bath
The reinforced PP plate is adopted for welding the flux solution bath of our steel wire hot-dip galvanizing line. A bath solution heating system is used in the galvanizing equipment to maintain the fluid at a proper temperature in according to production techniques. An air knife is available to retrieve the surplus solution.
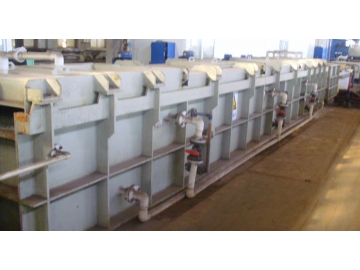
Drying oven
The drying oven is available in two types, electric heating type and gas heating type. A hot air circulation system is also designed. The frame of the furnace is welded by stainless steel, while the internal walls are welded by grade 316L stainless steel which can prevent the corrosion from the ammonium salt. Alumina silicate cellucotton is chosen as the high temperature resistant lining material for the purpose of heat conservation. In our steel wire hot-dip galvanizing line, the inner temperature is automatically maintained between 100℃ and 150℃.
Drying oven (electric heating)
Drying oven (gas heating)
Ceramic hot dip galvanizing kettle
The internal heating ceramic galvanizing kettle is a kind of advanced zinc-plating industry. Its heating efficiency could reach more than 80%. Limited zinc dross will be produced and the zinc consumption is also very low. The service life could be more than 10 years, while the temperature control accuracy is ±2℃. Thus the quality of the product from our steel wire hot-dip galvanizing line is quire stable.
Electric ceramic galvanizing kettle
Gas fired galvanizing kettle
Steel frame
The frame is made of reinforced steel which can provide great stability. A wire take-up machine is connected with the frame by bridging connection to facilitating the production of galvanized iron wire, galvanized steel wire, galvanized steel sheet, galvanized sheet metal, and so on.
Zinc coating wiping method of the steel wire hot-dip galvanizing line
- Asbestos clip wiping
Advantage: Thin zinc layer (40~100g/m²) can be achieved. The device has a simple structure, and needs a quite small investment.
Disadvantage: The thickness of the zinc layer is hard to control, leading to a big error and inconsistent wire. Besides, the operation is complex, so it needs human monitoring. The oil fume could pollute the environment. - Oiled charcoal for low speed galvanizing (zinc consumption: 150~300g/m2)
Advantage: The operation is quite simple and only a small investment is needed.
Disadvantage: The galvanizing speed should be less than 20m/min. The thickness of the zinc layer can not be controlled accurately. A large amount of oil fume will be produced, causing serious air pollution. - Nitrogen wiping
Advantage: This contactless wiping method can precisely control the zinc layer thickness by adjusting the gas pressure. It is suitable for high speed production. The operation is quite simple, and the zinc consumption is significantly lowered. In addition, no oil fume is produced during the whole process.
Disadvantage: The investment is larger than the other methods.
Nitrogen wiping equipment
Asbestos clip wiping
- Oiled charcoal wiping
Cooling
In our steel wire hot-dip galvanizing line, the air cooling and water cooling are combined together to cool the steel wire rapidly. Thus we can effectively control the thickness of the zinc-iron alloy layer, and enhance the smoothness of the galvanized steel wire.
Take-up machine
- The horizontal take-up machine is usually used for low/middle carbon steel wire with small wire diameter (0.7~4.0mm) and low wire coil weight (50~300kg). The suitable production speed is 10~30m/min.
- In our steel wire hot-dip galvanizing line, the inverted take-up machine is commonly used for low/middle carbon steel wire with regular wire diameter (1.6~5.0mm) and medium wire coil weight (500~1000kg). The production speed should be 15~45m/min.
- The spool type take-up machine is suitable for high/middle carbon steel wire with various wire diameter (1.6~8.0mm) and medium wire coil weight (above 1000kg).
- Inverted take-up machine
- Spool type take-up machine