Flexo Printing Press, TH Series
Request a Quote
In-Line Flexographic Printing Machine for Paper and Corrugated Board Printing
- Printing repeat: 500-1600mm
- Max. unwind diameter: 60" (1524mm)
- Max. rewind diameter: 60" (1524mm)
- Max. mechanical speed: 260m/min (850fpm)
- Substrate: 40-150gsm/100-350gsm
TH series in-line flexographic printing machine features a mechanical design that enables cylinder to be rotated in a reverse direction, this aims to keep operators safer. This in-line flexo press is typically suitable for food & beverage packaging printing, paper cup blank printing, paper bag printing, pharmaceutical box printing, and carton box pre-printing. The flexo printing machine can deliver a printing width range of 1000-1600mm and a repeat length range of 500-1600mm, able to handle printing operations for lightweight paper and corrugated board with premium printing quality.
Printing Examples
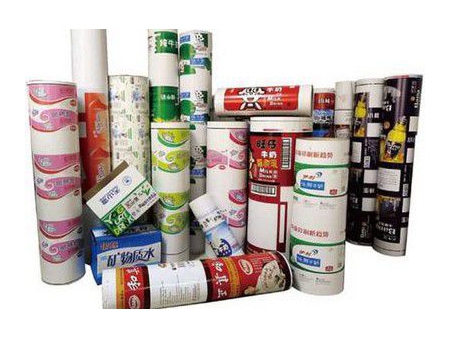
Custom Printed Roll Labels
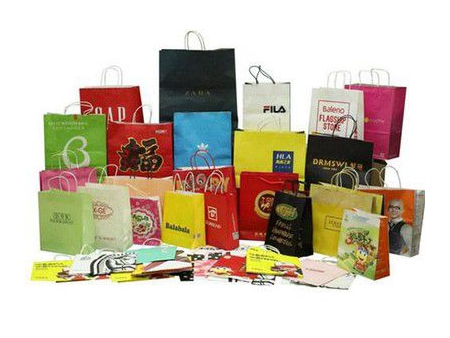
Custom Printed Paper Bags
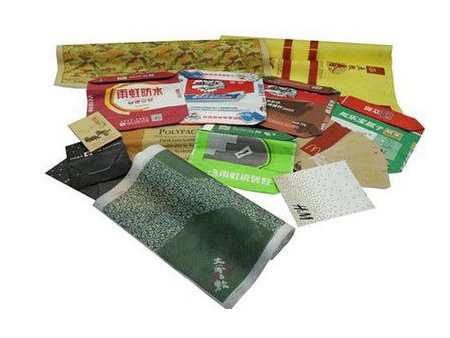
Printed Paper Shopping Bags
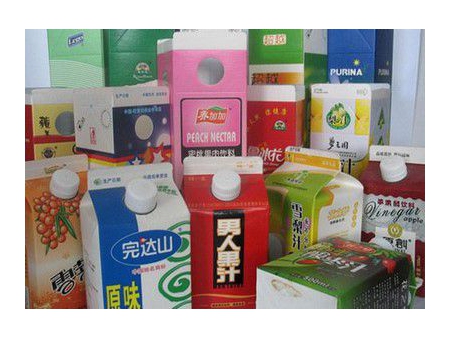
Printed Drink Cartons
Applications
- Food & Beverage Packaging Printing
- Paper Cup Blank Printing
- Paper Bag Printing
- Pharmaceutical Box Printing
- Carton Box Pre-printing
Features
- The design of upper web travelling enables printing process faster and more efficient;
- Independently controlled drying unit is equipped at each printing unit, significantly increasing drying efficiency while solving the print defects which commonly occur in water-based ink drying process;
- Adopting servo-driven motion technology allows to reduce machine vibrations and maintain high stability;
- The pressure of plate cylinder and anilox roll is fully controlled by servo motor, offering accurate control and easy operation;
- Remote fault diagnosis system provides operator with real-time machine running status, assisting users in quick troubleshooting to keep the machine running on a steady-state operation condition;
- Automatic pre-register setting allows for faster machine make-ready with less paper waste, efficiently lowering the cost to a minimum;
- Automatic butt splicer is used for non-stop unwinding and rewinding without slowing or stopping the process, greatly increasing production efficiency and reducing material waste;
- Optional drying units are available in steam, natural gas and electric heating methods;
- More configurations for your individual demands, such as gearless clamping unit, automatic web threading unit, automatic cleaning unit, etc.;
Details of Printing Unit
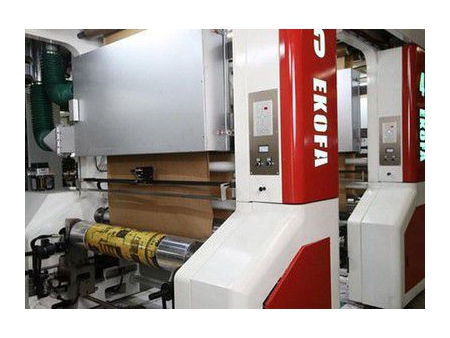
Model Options
-
- Max. web width
- 44.88" (1140mm)
-
- Max. printing width
- 42.52" (1080mm)
-
- Max. web width
- 51.57" (1310mm)
-
- Max. printing width
- 49.21" (1250mm)
-
- Max. web width
- 57.87" (1470mm)
-
- Max. printing width
- 55.51" (1410mm)
-
- Max. web width
- 65.35" (1660mm)
-
- Max. printing width
- 62.99" (1600mm)
Related products
Send Message
Most Recent
More
Other Products
Videos