Full-automatic Block Production Line
Full-automatic block production line is mainly formed by the integration of six systems including batching (dosing), mixing, molding, three-dimensional transportation, stacking and packaging. It can be used to produce all kinds of colorful pavement brick, cement block, water conservancy-related and hydraulic products, hollow block and concrete wall block, etc.
The full-automatic block production line adopts the closed-loop production process design and is composed of computer, various sensors, electromechanical hydraulic components and mechanical components.
The whole production process is controlled by computer and operated by mechanical automation. The entire process includes: the sensor measuring moisture content of raw materials, the moisture ratio by intelligent dynamic adjustment and mixing, wet material transporting & molding & production control, wet brick conveying, elevator-type lifting and stacking, automatic finger car transportation to curing kiln, the automatic recognition of finger car on empty kiln and kiln numbers, feeding the wet products into the curing kiln for curing, transporting dry products that have completed curing to the lowerator, lowering the dry products onto dry product conveyor in layers, transfer to the palletizing area, automatic palletizing gripper stacks the dry products onto the pallet in the unit of one cubic meter per stack according to requirements, transportation to the automatic packaging area by platform lorry and so on.
Composition systems- Batching (Dosing) system
Batching system is automatically controlled by computer. Once product formula is inputted and the computer can carry out automatic metering on different raw materials and then transfer the material into the mixing system. - Mixing system
Mixing system is applicable to the force mixing of all kinds of concrete products. The mixing time, the amount of water addition and door opening & discharging time are automatically controlled by the computer. And then the stirred material is fed into the molding machine by the conveyor. - Molding system
1).Molding system works by programmable logic controller (PLC) computer intelligent control and hydraulic transmission and vibration compression molding. And by computer control, the demands of producing different products and different materials can be achieved.
2).This system can display real time mechanical action and ensure that each mechanical action echoes with each other. It has the functions of automatic fault detection prompt, man-machine dialogue, remote control and so on.
3).According to users’ production requirements, this system can select different types and specifications of moulds, produce various cement blocks and other popular products in the market, and achieve the multi-purpose function of one machine. - Elevator
The elevator system adopts mechanical synchronous transmission and is under PLC computer control. It can smoothly raise the molded products to the ninth floor (floor tile and porous brick can rise to the eighteenth floor). - Finger car system
This system is operated by PLC computer control and finger car can start at low speed and run at high speed under the function of the same frequency converter. After the finger car is in place, it will slow down, brake and stop automatically and send the products into the curing kiln for curing. And then it will arrive in another kiln and take out the cured products to the lowerator. - Lowerator and palletizing system
1).The lowerator lowers the products to the brick conveyor and the products are transported to the palletizing area for palletizing. Then the piled up products are transported by forklift to the finished product stacking yard. The pallet is cleaned by the sweeper and the panel turnover (pallet tumbler) machine returns to the pallet stock of the molding machine.
2).The whole process can be controlled by manual, semi-automatic and fully automatic centralized control, which can realize a full-automatic production line integrating machine, electricity and liquid.
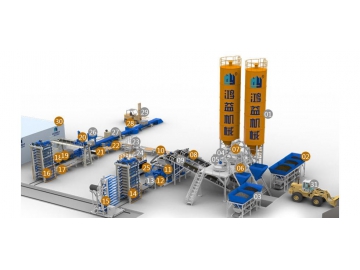
- Cement Silo
- Batching (Dosing) Machine I
- Batching Machine II
- Screw Conveyor
- Cement Scale
- Planetary Mixing Station
- Planetary Aggregate Mixer
- Belt Conveyor I
- Belt Conveyor II
- Horizontal Pallet Conveyor
- Block Making Machine
- Wet Product Conveyor
- Cleaning Machine
- Elevator
- Automatic Finger Car
- Lowerator
- Vertical Pallet Conveyor
- Tray Bin
- Finished Product Conveyor
- Cuber System
- Tray Cleaning Machine
- Pallet Tumbler (Panel Turnover)
- Pedestrian Ladder
- Hydraulic System
- Centralized Control System
- Horizontal Strapping Station
- Vertical Strapping Station
- Film Wrapping Machine
- Forklift
- Curing Chamber
- Wheel Loader
02
06
07
08
10
11
12
14
15
16
17
18
19
20
21
22
25
28
30